The clamping power alone in a tube bending machine should alert users to exercise the utmost precaution. Lincoln Brunner
If you use tube benders to manufacture parts, I’m sure you’re aware of the potential safety hazards they pose. Metal Works Custom Fabrication
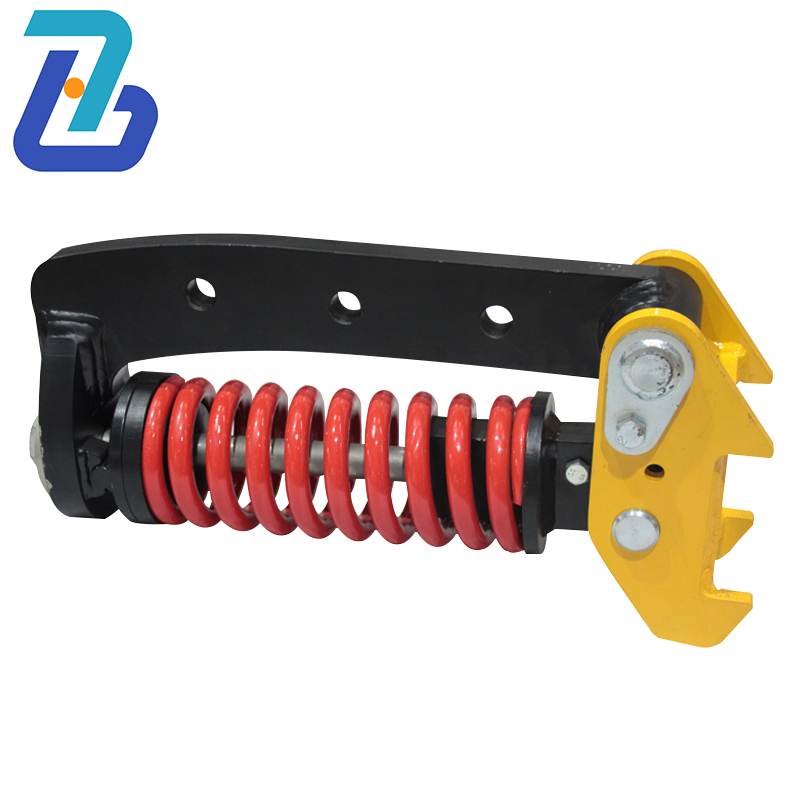
I wrote my very first article for TPJ after a customer called me in to help determine what had led to an accident in which an operator lost a couple of fingers after getting his hand caught in the clamps of a machine.
How can this happen? Well, it’s important to remember that the tremendous force it takes to form steel tubing into a bent shape creates serious potential for harming a human. For example, a typical hybrid machine capable of bending 3-in. tubing often uses a 4-in. hydraulic cylinder for clamping the pressure die. At 2,000 PSI of hydraulic pressure, that cylinder closes with 25,000 lbs. of force—more than enough to seriously harm a person.
Unfortunately, in late 2023, our industry was shaken when an operator lost her life after an accident involving a CNC tube bender. The woman, Taylor Kendrick, died on the scene in a factory when she was crushed in the machine. As word has gotten around, many of our customers have begun a review of their own safety practices and have updated their safety policies.
We encourage our customers to review and update their tube bender safety practices throughout the year. But when things slow down at the end of the year, that’s the time to really dig deep into how to improve equipment and practices. When operators return from the holidays in the New Year, it’s a great time to review your safety practices and implement new policies and procedures.
Here are a few things to consider regarding CNC tube benders when conducting your own safety review.
If you are still using pressure mats as the main devices to prevent bender movement when an operator is in hazardous areas, make sure they offer enough coverage.
Often, we find that mats have been placed to allow operators to stand behind or off to one side and still reach into the clamping areas of a bender with their hands and arms—or that the mats have been moved to areas where they can be completely avoided. And because safety mats are easily damaged when tooling or parts get dropped on them, we often see them in place but bypassed and inoperable.
Make sure your safety mats are bolted to the floor and placed so that an operator cannot reach into the clamping area without stepping on a mat. Teach your operators not to straddle or lean over the mats, and make sure they understand that the part being produced may extend beyond the coverage provided by the mats and to stand well clear.
Floor scanners project a laser a few inches above the floor. When the laser beam is broken within a certain area, the machine stops or is prevented from starting.
When properly positioned and programmed, floor scanners can provide a larger coverage area than safety mats, and the shape of the area is not limited to a rectangle. These devices are much harder for operators to defeat, and some scanners can offer multiple selectable zones, so the coverage area can be quickly and easily changed to cover different part shapes.
Make sure your floor scanners are bolted into place to ensure consistent coverage. Mark the covered area clearly on the floor so that operators know where they cannot stand. And make sure the programmed area does not have “shadows”—areas of coverage where an operator could be in danger but still be undetected by the scanner.
Some areas of a bender may be impossible or impractical to protect using safety mats or floor scanners. Consider installing fencing to prevent someone from stepping or reaching into these areas.
If these areas need frequent access for machine adjustment or maintenance, gates with switches or keys that prevent the machine’s operation are available. If you install fencing, make sure the gate cannot be closed and the machine operated with someone in the safety area. Don’t forget to include fencing around the carriage and its mechanical drive systems, hydraulic motors and couplings, and mandrel mechanics.
Emergency stop buttons should stop all movement of the machine and turn off power to any device that has the potential to move.
Footswitches allow an operator’s hands to be free while loading and unloading a tube from a bender. However, because they free operators’ hands, they also can create a situation that may allow operators to place their hands in a dangerous area.
Bolting a footswitch to the floor ensures operators cannot push it with their feet while reaching into the machine, enhancing safe operation. We often install two footswitches: one that only operates closing and opening of the collet and one that starts the auto cycle.
On most CNC tube benders, opening and closing the collet is considered a safe operation in which to grip the tube, even if someone is standing inside the safety area. By using a footswitch that is dedicated to the collet, an operator can load a tube while standing near the machine and then step out of the danger zone to press the second footswitch to start automatic operation from a safe location.
As the safety systems of tube benders are upgraded, we often hear operators gripe that it is harder to set up a machine for production or that the new safety devices will slow down their production rate.
However, almost always, operators can find ways to set up a machine that at least meets the previous production levels—and often exceeds them. Most of the times we hear of an injury on a tube bender, the safety measures in place were somehow bypassed.
Keep in mind these important tips:
See More by Jay Robinson
Read more from this issue
Subscribe to The Tube and Pipe Journal
The Tube and Pipe Journal became the first magazine dedicated to serving the metal tube and pipe industry in 1990. Today, it remains the only North American publication devoted to this industry, and it has become the most trusted source of information for tube and pipe professionals.
Easily access valuable industry resources now with full access to the digital edition of The Fabricator.
Easily access valuable industry resources now with full access to the digital edition of The Welder.
Easily access valuable industry resources now with full access to the digital edition of The Tube and Pipe Journal.
Easily access valuable industry resources now with full access to the digital edition of The Fabricator en Español.
On this episode of The Fabricator Podcast, Philadelphia-based welder and trades advocate Pa'Trice Frazier joins host Dan Davis...
© 2024 FMA Communications, Inc. All rights reserved.
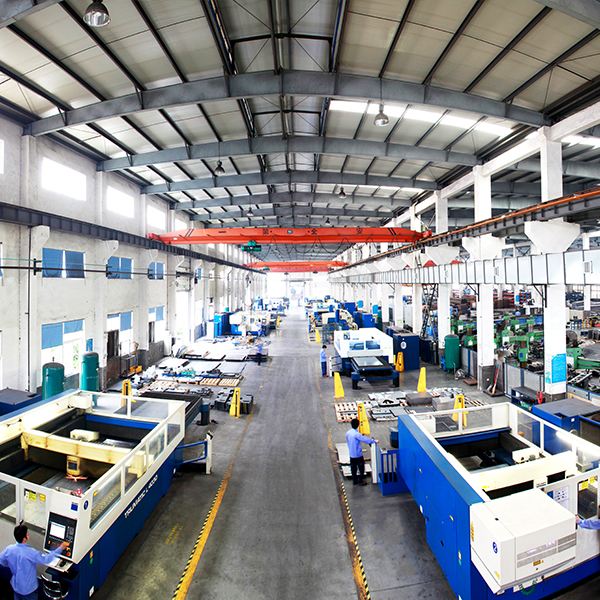
Plasma Cutting Aluminium Not yet registered? Sign up