Building horsepower is an inherently dirty endeavor. Whether it’s gas or diesel-powered engines and parts, this industry’s men and women see their fair share of grease, grime, oil, rust, paint, and more. While they’re completely okay working within that environment, cleanliness is arguably the most important piece of the pie when it comes to getting a finished engine ready for the customer. Related Articles - Degreeing the Camshaft and Checking Valve-to-Piston Clearance - Designing a Better LS Engine - The Importance of a Good Valve Job
Whether building a brand-new engine or rebuilding an existing engine, cleaning is the first step in the process. Contaminants can easily harm both the component and the equipment when it comes time to machine and assemble. Brass Cnc Cutting
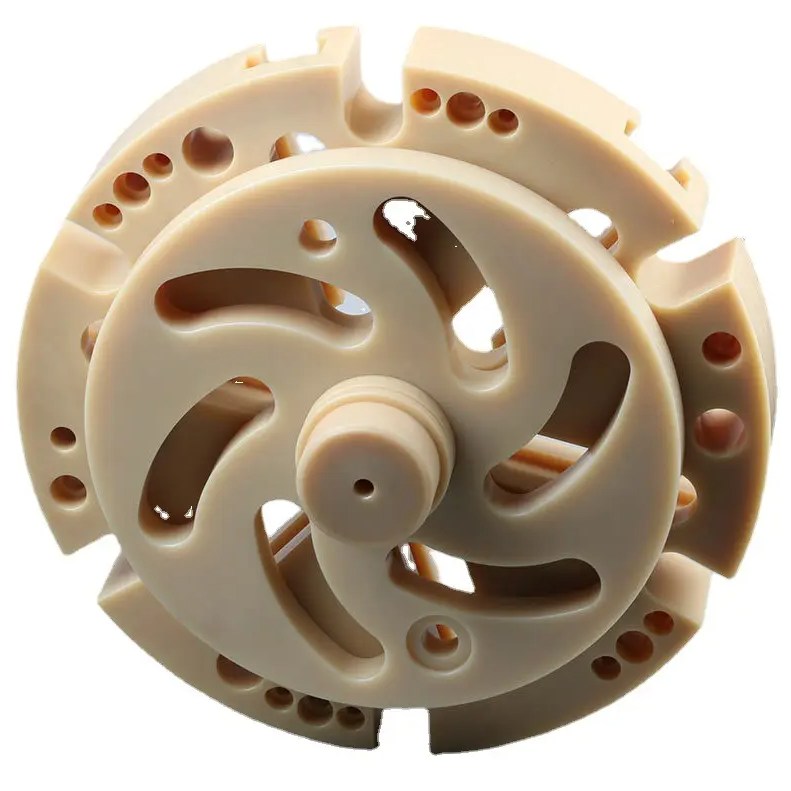
In engine building, every detail matters. The most minuscule impurities or irregularities can mean the difference between a powerhouse of performance and a premature engine failure. As engine builders relentlessly pursue perfection, the quality of the components they assemble becomes a non-negotiable benchmark. As such, engine shops are spending more time than ever before on the cleaning process.
Unfortunately, there isn’t just one machine that can do all the cleaning work required for an engine shop – most shops have a number of cabinets, tanks, ovens – all with different functions and cleaning methods. Using an engine block, for example, there are typically three stages to cleaning an engine component.
“We’ve got our cleaning processes down,” says Jesse Warren of Warren Diesel Injection. “Every block that comes in goes in the oven first to get off the excess crud and such.”
The baking process helps to burn out the oils, carbon and other contaminants out of raw castings and cores, loosening the materials so they will come off easier in the subsequent processes. With cast iron, the oven can go to 700 degrees F.
Next, the block will go through a media blasting machine. Media blasting machines combine compressed air, small abrasive materials (media) and specialized equipment to quickly prepare a surface for refinishing or other purposes. Media blasting is a very efficient way of removing debris from the surface of parts or preparing a surface for painting or other finishes.
The team at Warren Diesel Injection uses an ARE Industries HB-41 head and block blaster, which uses tiny S-230 steel beads for media. As mentioned, different machines can use a variety of different media, which have different purposes and results in how they clean. Steel shot media is used for cast iron engine components, while glass beads are used for aluminum components. Media such as baking soda can be used on any surface to remove a plethora of substances.
After components get done with a media blast cabinet cleaning, parts usually get some sort of water-based cleaning method. Drew Pumphrey of D&J Precision Machine uses a Renegade parts washer machine for his final, water-based cleaning routine for large parts like blocks and heads. According to Drew, the Renegade parts washer saves the shop the most time before final assembly.
These machines use high-pressure water jets and heat to clean off the fine contaminants left on the block or other components. These machines typically rotate the parts while they are sprayed so that debris will fall out and water won’t stand still in certain areas and crevices. After the wash, shop owners can air dry the part and begin the painting or assembly process.
Another popular cleaning method for both large and small components is the use of ultrasonic cleaning machines. Ultrasonic LLC offers tabletop, mobile and lift table machines, which offer different capacities depending on the size of the component you are looking to clean. Just as with anything else in engine building, the right machine will do the job better.
Lift table machines are designed for large and/or heavy parts like blocks, and large-capacity parts cleaning. They are built low to the ground, so they’re not only easy to use, but they’re easy on the back. These machines are much larger, with 115-gallon and 210-gallon volumes for the Ultra 3800FLT and Ultra 6000FLT, respectively.
Tabletop machines are used for smaller parts and mobile units are handy if you need to move in and out of different areas of the shop. While an ultrasonic cleaner might share similarities with a hot tank, its distinguishing feature lies in the generation of cavitation, involving the formation and collapse of bubbles in the cleaning solution.
Ultrasonic systems employ a transducer to transform electrical energy into sound waves, consequently producing cavitation bubbles responsible for cleaning the components. These bubbles swiftly form and collapse across the surface, effectively accessing small crevices and galleys. As these bubbles implode, they draw contaminants and particles away from the surface, relocating them to the upper layer of the solution.
Companies like Safety-Kleen offer several options for cleaning equipment, from ultrasonic machines to spray washers and blast cabinets, as well as both automated and manual varities. Spray washers deliver highly efficient cleaning with a smaller footprint and are ideal for in-line cleaning applications or areas with less available floor space. Parts rotate on an automated, friction-drive turntable to get complete 360-degree coverage for precise and effective parts cleaning. Top-loaders are equipped with automatic oil skimmers and fluid-level shut offs to protect the heater elements.
In an aqueous cleaning process, it’s very important to choose the right chemistry for the job. Safety-Kleen offers an exclusive line of ArmaKleen chemistries, which are multi-metal safe and can handle a variety of soils. They’re also rust prohibitive and have a variety of pH ranges.
For example, the ArmaKleen M-100 BCR (Baked on Carbon Remover) is a low pH, caustic-free cleaner designed to attack and remove baked on carbon and other tough soils from steel and soft metals like aluminum engine blocks and other aluminum alloy components. M-100 is designed to not only clean parts, but also brighten them to like-new conditions.
No matter what cleaning method you employ, it’s likely not just one. And, it can’t be overstated how important the cleaning machines are in the modern engine shop. Shop owners who prioritize effective and efficient cleaning techniques will find success in a more streamlined process. EB
Check out the latest shop solutions from builders around the country.
Engine Builder and Engine Pro present Shop Solutions in each issue of Engine Builder Magazine and at enginebuildermag.com to provide machine shop owners and engine technicians the opportunity to share their knowledge to benefit the entire industry and their own shops. Those who submit Shop Solutions that are published are awarded a prepaid $100 Visa gift card. Submit your Shop Solution at [email protected]. You must include your name, shop name, shop address and shop telephone number. Submitted Shop Solutions not published will be kept on file and reevaluated for each month’s new entries.
When it comes to choosing the right fuel for your vehicle, several factors should be taken into consideration. These factors include the vehicle’s engine design, manufacturer recommendations, intended usage, and personal preferences.
Billet aluminum has a lower yield strength or higher modulus of elasticity, meaning it will flex, or absorb energy easier under tension or stress than cast aluminum, without incurring permanent damage.
Many times, the flange diameter of the rod nuts will contact the radius around the nut seat on some rods. Some jobs may not warrant the expense of spot facing the nut seat on the connecting rods. In that case, it can be quicker and more effective to just machine a chamfer on the ARP rod nuts.
Several manufacturers named automation as one of the biggest continuing trends surrounding CNC equipment these days, and it’s clearly a key contributor to a CNC machine’s ability to do more without human interference.
Most engines are internally balanced, meaning all weight adjustment is done on the crankshaft counterweights. However, some stock and modified engines require external balancing due to an increased stroke or larger pistons, and the crankshaft counterweights that would be required to offset the increased inertia simply don’t fit inside the crankcase.
Unlike standard spray cabinet washers, immersion cleaning exposes all surfaces of the part, including blind holes and small crevices, to the cleaning solution.
A written warranty provides benefits for you and your customer. It sets expectations, protects both parties and is a great marketing tool that encourages repeat business.
High-frequency fatigue, also known as harmonics, are a ubiquitous challenge in racing engines and can potentially wreak havoc on the valvetrain if left unchecked. Well-designed valve springs play a pivotal role in managing this, ensuring essential stability, and minimizing wear on valvetrain components.
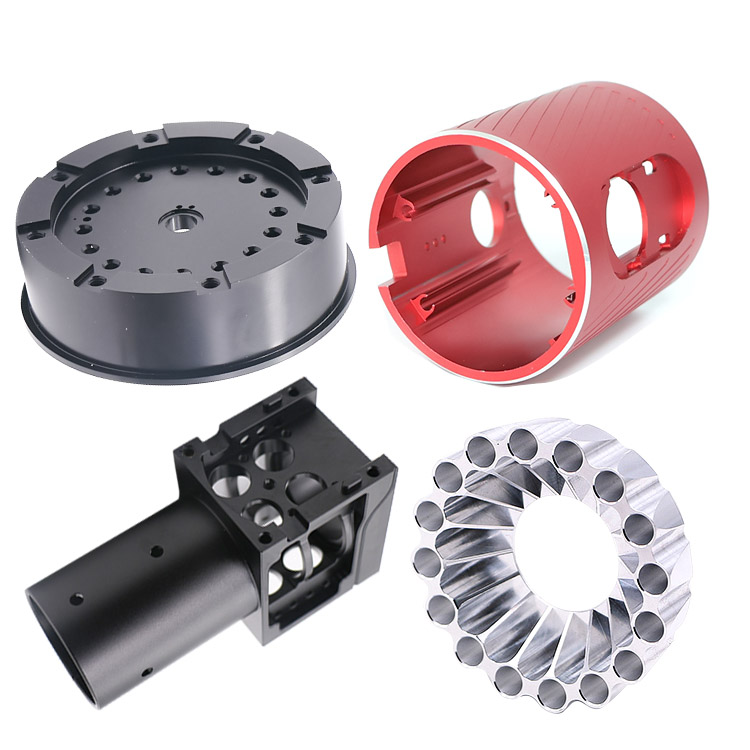
Complex Cnc Machining Content for engine professionals and enthusiasts